Understand the basic knowledge of roof tile forming machine
You will learn
What is a ridge tile forming machine?
The ridge tile forming machine is a mechanical equipment specifically used for producing ridge tiles (i.e. the tiles used to connect the highest point of the roof to the slopes on both sides). This type of machine usually uses cold bending technology to press and bend metal sheets or other materials according to predetermined specifications and shapes, thereby forming decorative or functional tiles suitable for building roof ridges.
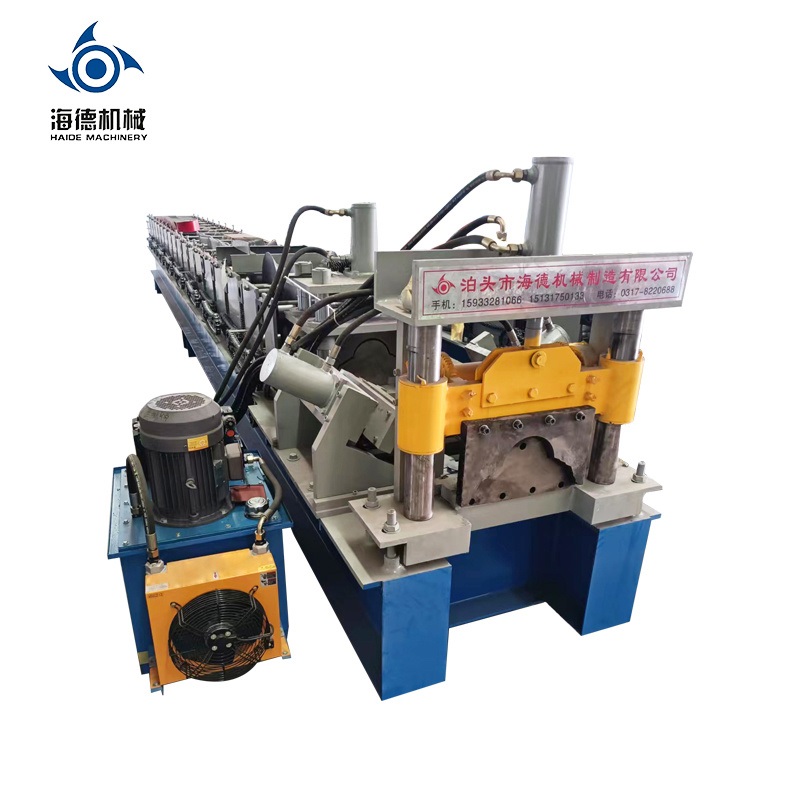
What is the workflow of the roof tile forming machine?
- Raw material preparation: Firstly, prepare the raw materials for making roof tiles, usually metal sheets such as color coated steel plates, galvanized steel plates, etc.
- Uncoiling: Install the rolled metal sheet onto the unwinding rack of the forming machine, and unfold the sheet through the unwinding machine.
- Straightening: In order to ensure the flatness of the board in subsequent processes, a straightening device is needed to eliminate the bending and wavy deformation of the board during the rolling process.
- Forming: The board is formed by a series of pre-set roller molds arranged at certain intervals, and gradually bent into the shape of a roof tile through rolling. This process is commonly referred to as rolling forming or continuous forming.
- Cutting: After the board is fully formed into the desired shape of the ridge tile, it will be cut to a predetermined length by a cutting device to obtain a single finished ridge tile.
- Collection/output: The cut roof tiles are collected at designated locations or directly transported to the next process.
- Quality inspection: During the production process, it is necessary to regularly inspect the quality of the roof tiles to ensure that the dimensional accuracy, surface quality, and shape meet the requirements.
- Packaging and Storage: Qualified roof tiles will be packaged and stored in a suitable environment, waiting for further transportation or installation.
How to improve the manufacturing efficiency of the roof tile making machine?
- Optimize device performance:
-Use more efficient motors and transmission systems to reduce energy loss.
-Select high-quality bearings and transmission components to reduce wear and failure rates.
- Improve mold design:
-Optimize the design of the mold to make it more durable and easy to maintain.
-Improve the accuracy of molds, reduce molding errors, and lower scrap rates.
- Improve automation level:
-Introduce automated control systems, such as PLC control, to achieve more precise speed and position control.
-Using an automatic loading and unloading system to reduce manual operation time and labor intensity.
- Strengthen quality control:
-Implement strict quality management standards to ensure that every step of the process achieves the expected results.
-Use online detection equipment to promptly detect and correct deviations in the production process.
- Improve production process:
-Optimize the production process, eliminate unnecessary steps, and simplify the manufacturing process.
-Implement lean production management, reduce waste, and improve the overall efficiency of the production line.
The main functions and specifications of the Jiaochi forming machine
Main functions:
- Sheet metal forming: The sheet metal is pressed into a specific shape through a series of roller molds.
- Efficient production: With a high degree of automation, it can achieve continuous production and improve production efficiency.
- Anti leakage performance: The produced roof and wall panels have good sealing performance and are suitable for buildings with high waterproof requirements.
- Diversified applications: In addition to conventional flat panel production, it can also be used in conjunction with other equipment (such as arching machines) to produce special shaped panels, such as beamless arched roofs.
- Automation control: Usually equipped with PLC control system, it can achieve precise control of the production process.
Specifications:
-Size: The size and weight of the corner forming machine vary depending on the manufacturer and specific model. For example, some models have installation dimensions of 11000mm × 1300mm × 1500mm.
-Power demand: Depending on the equipment, the main motor power may be 4KW and the hydraulic station power may be 3KW.
-Molding speed: The molding speed is approximately 9 meters per minute.
-Sheet thickness: The thickness range of machinable sheets is usually between 0.3 and 0.8 millimeters, depending on the design of the equipment.
-Processing width: Depending on the machine model, the unfolded width of the processed sheet metal may vary from several hundred millimeters to over one meter, and the effective width of the formed sheet metal is smaller than the unfolded width.
-Control system: Using fully automatic industrial computer PLC frequency conversion control to achieve stable production and precise size control.
-Additional features: Some high-end models may offer additional functions such as automatic measurement, automatic cut-off, etc.
The benefits of using a ridge tile forming machine
- High production efficiency: Roof tile forming machines usually have high-speed forming capabilities and can continuously produce a large number of roof tile products, greatly improving production efficiency.
- Good cost-effectiveness: Due to the high degree of automation, it reduces labor costs; Meanwhile, by precisely controlling the amount of materials used, material waste has been reduced and overall production costs have been lowered.
- Stable product quality: Machine production can maintain consistent product quality, reduce errors caused by human factors, and ensure that the size, shape, and quality of each roof tile meet uniform standards.
- Strong adaptability: Different specifications of roof tiles can be customized according to customer needs to meet the requirements of different building styles and sizes.
- Easy to operate: Modern roof tile forming machines are usually equipped with advanced control systems, such as PLC (Programmable Logic Controller), making the operation simpler and more intuitive, reducing the difficulty of operation.