Understand the basic knowledge of angle iron keel forming machine
What is angle iron keel forming machine?
Angle iron keel forming machine is a mechanical equipment specifically used for producing angle iron (angle steel) keels. Angle iron is a commonly used profile in construction and manufacturing industries, with an L-shaped cross-section, commonly used for making frame structures, supports, connectors, etc. Keel refers to the skeleton structure that plays a supporting role in buildings, such as metal or wooden frames in ceilings and partitions.
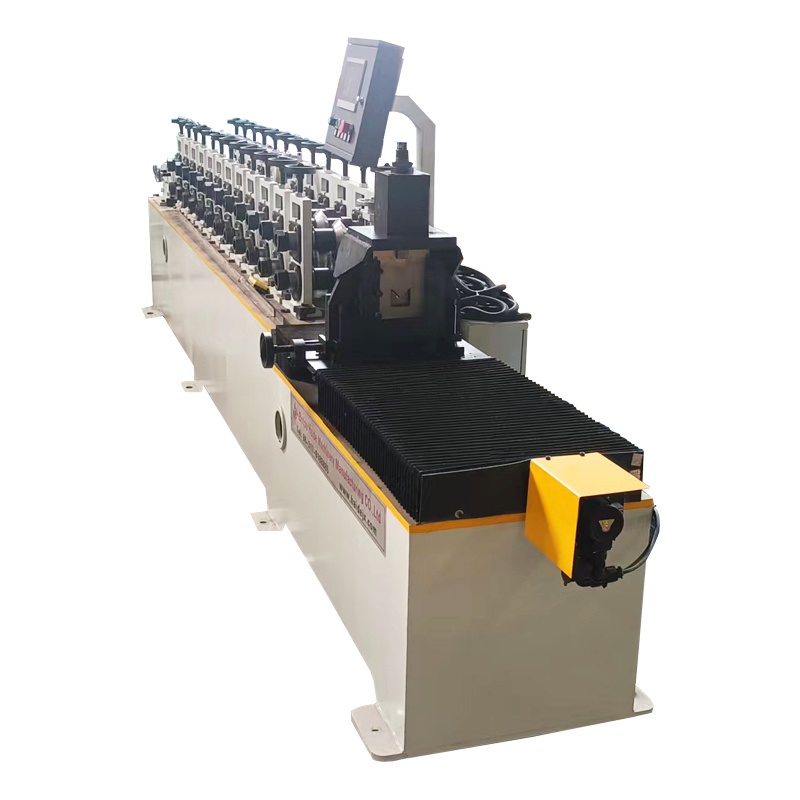
The workflow of angle iron keel forming machine?
- Raw material preparation: First, prepare the sheet metal that needs to be processed, usually steel or galvanized sheet metal. The thickness and width of the sheet metal need to meet the design requirements of the equipment.
- Loading: Place the prepared sheet at the entrance of the machine and feed it into the forming machine manually or automatically.
- Forming: After entering the forming machine, the sheet will pass through a series of forming rollers. These rollers are arranged in a predetermined order, and with each set of rollers, the board undergoes a certain degree of bending deformation until it finally forms the required L-shaped or other specific shaped angle iron keel.
- Calibration: During the molding process, in order to ensure the dimensional accuracy and flatness of the keel, some machines are also equipped with calibration devices to adjust the position and shape of the board.
- Cutting: After the sheet is formed to the required length, the molding machine will automatically cut it into the set size. This process is usually accomplished through hydraulic shearing or rotating cutting tools.
- Punching (optional): According to the requirements, the forming machine can also be equipped with punching devices to punch holes with fixed spacing on the keel for subsequent installation and use.
- Cutting: Finally, the formed angle iron keel will be transported to the designated location and collected and organized by manual or automated systems.
- Inspection and packaging: The formed angle iron keel also needs to undergo quality inspection to confirm that there are no defects before packaging, preparing for storage or shipment.
How to improve manufacturing efficiency of angle iron keel forming machine?
- Automated production: Angle iron keel machines usually have highly automated characteristics, which can achieve automated operations from feeding, forming, cutting to unloading, reducing the time and labor costs of manual intervention.
- Continuous operation: The molding machine can work continuously, only requiring regular replacement of raw material rolls, which makes the production process smoother and avoids efficiency losses caused by frequent shutdowns.
- Quick mold change: Some advanced angle iron keel machines are designed with quick mold change systems, which can replace different molds in a short period of time to adapt to the production of products of different specifications, reducing the time for mold change.
- Precise control: Through a computer control system, each step of the processing parameters can be precisely controlled, such as feed rate, bending angle, etc., to ensure product consistency and high quality.
- Multi station design: Some molding machines are equipped with multiple stations, which can complete multiple processes such as molding, punching, cutting, etc. on the same machine, reducing material handling time and improving production efficiency.
- Reduce waste: By effectively utilizing raw materials and precise cutting techniques, the generation of waste in the production process can be minimized to the greatest extent possible, thereby improving material utilization.
- Easy maintenance: The modern angle iron keel machine design considers maintenance convenience, and regular maintenance can ensure long-term stable operation of the machine, reducing downtime caused by malfunctions.
- Data management: Some high-end molding machines also integrate data management systems, which can optimize the production process by monitoring production data in real time, discovering potential problems in a timely manner, and taking measures to solve them.
Main functions and specifications of angle iron keel machine
Main functions:
- Forming: The flat steel is bent into the desired shape of angle iron through a series of forming rollers.
- Cutting: Cut the formed angle iron according to the predetermined length.
- Punching: Punching holes with fixed spacing on the angle iron for easy fixation during installation.
- Slotting: In some cases, it is necessary to make slots on the angle iron for use with other components.
- Bending: For angle irons that require special shapes, the equipment may also have bending capabilities.
- Automation control: Most modern angle iron keel machines use PLC control systems to achieve automated production processes.
Specifications:
- Production capacity: Depending on the equipment, the production capacity can range from tens of meters per hour to hundreds of meters per hour.
- Applicable materials: Generally suitable for cold-rolled or galvanized sheets with a thickness between 0.4mm and 2.0mm.
- Material width: The width of materials that the equipment can handle may also vary, with a common range of 50mm to 200mm.
- Molding size: Different specifications of angle iron keel can be produced, with common sizes including 38mm × 38mm, 50mm × 50mm, etc.
- Power consumption: Depending on the size of the device and the degree of automation, power consumption can range from several kilowatts to tens of kilowatts.
- Equipment size: The length, width, and height of the equipment vary. Small equipment may only be a few meters long, while large production lines may reach tens of meters or even longer.
- Weight: The weight varies from several hundred kilograms to several tons depending on the size of the equipment.
- Control system: PLC programming controller is usually used, combined with touch screen operation interface to achieve human-computer interaction.
- Safety protection: equipped with various safety protection devices, such as emergency stop button, overload protection, etc.
The benefits of using angle iron keel machine
- Improve production efficiency: The highly automated angle iron keel machine can achieve continuous production, greatly shorten the production cycle, and improve production efficiency.
- Ensure product quality: Through precise molds and control systems, the angle iron keel machine can ensure that the size of the produced keel is consistent and the accuracy is high, reducing the errors that may be caused by manual operation.
- Save labor costs: Automated production reduces reliance on manual labor, lowers labor costs, and also reduces quality issues caused by human factors.
- Reduce material waste: Accurate cutting techniques and reasonable discharge plans can maximize the use of raw materials, reduce waste generation, and thus lower material costs.
- Improve safety: Automated equipment reduces the opportunity for workers to directly come into contact with hazardous components and lowers the risk of work-related accidents.
- Strong flexibility: By changing molds or adjusting parameters, the angle iron keel machine can produce keels of different specifications to meet diverse market demands.
- Easy to maintain: Modern angle iron keel machines are usually designed to be easy to maintain, simplifying daily maintenance work and extending equipment service life.
- Environmentally friendly: Automated production processes reduce unnecessary resource waste and help companies achieve their goal of green production.
- Enhancing competitiveness: Using advanced production equipment can improve the production capacity and product quality of enterprises, and enhance market competitiveness.
- Data Management and Analysis: An integrated data management system can help enterprises better manage production data, optimize production processes, and promptly identify and solve problems.